Dielectic fluid transforms to a conductive channel to deliver the spark that vaporizes the metal when the electric discharge takes place. Photo courtesy of Makino.
Three ingredients are key to successful sinker or ram electrical discharge machining (EDM) cutting—the machine, the electrode tooling, and the dielectric fluid. The equipment and the electrode typically get the most attention. The fluid, an oil designed specifically for the process, not so much. But it should. Agie EDM Wear Parts
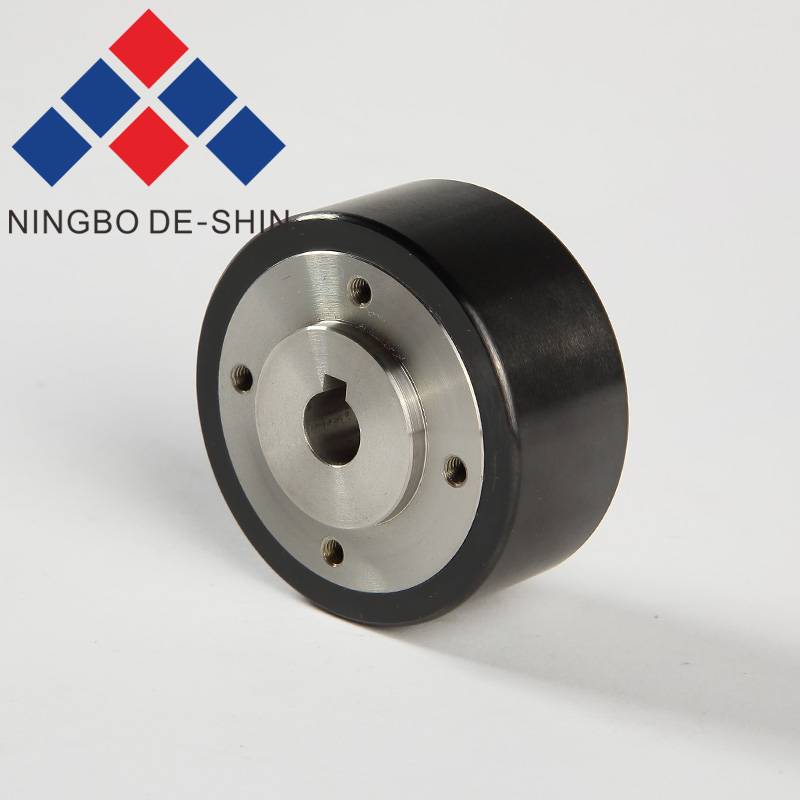
When the fluid degrades, machine performance declines. Cutting speeds slow and quality and surface finish suffer. Filling the machine tank with a petroleum-based oil is not a one-and-done deal.
The dielectric fluid, a critical and fundamental component of the process, establishes the medium in which the machining discharge spark energy is finely controlled, balanced, and delivered to the workpiece. When the workpiece and electrode are submerged in the fluid for the machining process, the fluid transforms from an insulator to a conductive channel to deliver the high-power discharge spark energy that vaporizes the metal.
And the fluid flushes the miniscule chips formed when the vaporized metal condenses back to solids away from the workpiece to clear the spark gap zone before the next electric discharge cycle begins. To attain and maintain optimal EDM efficiency, the dielectric fluid characteristics need to be clean and stable.
“Depending on your application, your standard petroleum-based fluids will probably have an operational lifespan of three to five years,” said Brian Pfluger, EDM product line manager at Makino. “Once that fluid begins to break down, it can no longer support and maintain the stability of the spark gap needed for an efficient EDM process.”
Performing a lot of high-amperage burns can cause the fluid to break down somewhat faster than when working with low amperage, Pfluger said, but basically, the amount of use doesn’t significantly lengthen or shorten the fluid’s lifespan.
“The chemical nature of a standard petroleum-based EDM fluid causes it to break down regardless of the amount of use. It’s like milk—it has a finite shelf life,” he said. “When using old, broken-down fluid, the machine’s adaptive control is always fighting to stabilize the process and overcome the lack of proper fluid characteristics needed for stable EDM. It can have a long-reaching, dramatic, negative effect on equipment performance, including speeds, accuracy, and surface finish capabilities.
“The biggest detriment is to cycle time. It can be upwards of 50 per cent slower. When the machine isn’t cutting as well as it used to, it can be because the fluid is broken down and depleted. Machine capability will return when the fluid is changed. For comparison, is it realistic for a Formula 1 race car to perform at optimal competitive levels using 10-year-old oil? A sinker EDM machine may not be much different.”
Since EDM is a fairly slow-moving machining process and the fluid degradation is also a typically slow process, the gradual loss of productivity can be difficult to detect. Changes in surface finish might be a bit more apparent.Fluid colour can indicate that it is time for a change. Pfluger said, “Over time the fluid will usually change colour. It starts out clear or maybe a light brown, and as it breaks down, it takes on a darker, murky colour. Some of the oils can also pick up an odour as they degrade.”
Oxygen and heat are integral in the oxidation process of the fluid. The natural process of oxidation occurs through heat transfer during the EDM process as well as through external influences from the environment. Oxidation is the biggest enemy of petroleum-based fluids, according to Brett Reynolds, senior applications engineer for Blaser Swisslube.
Dielectric fluids need to be kept clean to deliver the spark to the material and remove the metal residue created by the process. Photo courtesy of Makino.
“The oxidative levels are determined by measuring the total acid number (TAN), which indicates the degree of oxidation due to in part organic acids produced during the machining process. The TAN increases as the fluid becomes more oxidized. Generally, a TAN of greater than 1.5 is a good indicator that the oil has reached its life expectancy.
“There are things you can do to help prevent oxidation,” said Reynolds. “Eliminate cross-contamination points. For example, be sure that parts are clean before immersing for EDM. Remove oils or water-soluble coolants used for previous processes.”
Fluid also can become hydrolyzed from cross-contamination or water from a high-humidity environment. A controlled shop environment is ideal. The old adage that water and oil don’t mix is apt when it comes to EDM processing.
As a dielectric fluid decomposes, sticky, gummy residues similar to a varnish form within the fluid, said Edward Jones, COO and technical director at Hangsterfer’s Laboratories Inc. “These varnishes interfere with the electrical discharge process. It slows the process of removing the metal particles created by the process from the cutting zone. Then amperage needs to be reduced, the process slowed, to allow for chip removal so they don’t interfere with metal removal from the next electrical discharge.”
That same residue can also adversely affect the fluid filtering process, he continued. “Advanced machines have very good filtration to remove the impurities—the metal particles. Varnish formation in the fluid forces the filters to remove decomposition impurities as well as the solid particles. So the filters become clogged, less efficient, and don’t last as long.
“There is normally a pressure drop if the filter is blinded off. It becomes soiled and causes too much back pressure and resistance for the fluid to freely flow through it for filtering.”
If pressure drops, the filter should be changed. And anytime the oil is changed, the tank should be wiped down and the filter should be changed to avoid contaminating the fresh fluid.
“Terminology of synthetic gets a little grey,” said Jones. “Almost all the fluids can be considered synthetic in someone’s point of view. Petroleum can be refined in such a way to remove the impurities and actually make it as good as vegetable oil, and that can be considered synthetic in some cases. Then there are fluids that are partially petroleum-derivative and partially synthetic-derivative—fluid engineered in a lab.” And there are fluids that are full synthetics.
As oils progress up the refinement scale, the amount of refinement and alteration of the hydrogen chain increases. Their lifespan increases, and their stability can contribute to higher equipment productivity. “It’s the very uniform hydrogen chain size of the oil molecules that makes the high-performance fluids unique. Consistent links in the hydrogen chain gives the oil a much higher degree of oxidative stability. Synthetic-base stocks also have a narrow viscosity index, which means that the thickness of the oil will fluctuate very little when its temperature increases or decreases,” said Reynolds.
A low viscosity not only aids in moving the debris away from the cutting zone, but assists in removing the heat generated by the machining process. Keeping the workpiece at a constant temperature to avoid material expansion or shrinkage during machining contributes to process accuracy.
Highly refined fluids that include synthetics have been credited with being more operator- and environment-friendly. “With a higher-engineered fluid, fewer solvents evaporate into the air that an operator can breathe in. The chemical makeup of a less refined fluid can also cause white hands when an operator submerges his hands in the dielectric fluid—actually take away some of the fat from the skin and cause it to turn white,” Jones said. “They also have a higher flash point, which is safer.
“Technology is making these fluids pure. There are molecules that can be changed in a way that performs just as well or better than the traditional fluids and minimizes the environmental impact.”
By side-stepping the degradation issues, highly refined, partially or fully synthetic fluids may not need to be changed, just occasionally topped off. Filters, however, will continue to collect the small metal bits and will need to be periodically replaced.
“Some manufacturers use the latest machines and tooling technologies but use 1970s dielectric fluid technologies that might not meet the needs of high-performance machines,” said Jones. “They should look at the new fluid technologies. They can increase EDM productivity by 30 per cent.”
Blaser Swisslube Inc., 845-294-3200, www.blaser.com
Hangsterfer's Laboratories Inc., 800-433-5823, www.hangsterfers.com
Makino, 800-552-3288, www.makino.com
See More by Sue Roberts
Sue Roberts, associate editor, contributes to both Canadian Metalworking and Canadian Fabricating & Welding. A metalworking industry veteran, she has contributed to marketing communications efforts and written B2B articles for the metal forming and fabricating, agriculture, food, financial, and regional tourism industries.
Roberts is a Northern Illinois University journalism graduate.
Read more from this issue
Find Canadian Metalworking on Facebook
Find Canadian Metalworking on Twitter
Keep up to date with the latest news, events, and technology for all things metal from our pair of monthly magazines written specifically for Canadian manufacturers!
Easily access valuable industry resources now with full access to the digital edition of Canadian Metalworking.
Easily access valuable industry resources now with full access to the digital edition of Canadian Fabricating & Welding.
In this customer spotlight, we feature Photon Automation of Greenfield, Indiana. CEO William Huffman shares with us why they chose Hurco as their machine tool builder and how Photon Automation’s revolutionary patented laser technology is powering emerging markets today.
© 2023 FMA Communications Canada, Inc. All rights reserved.

EDM Brass Wire 900N Not yet registered? Sign up