It’s something that has probably happened to more than one of us over the years, there’s an unmissable opportunity at the machinery auction or on eBay, with the small snag that it weighs a ton and requires a flatbed truck to transport. A big lathe, a bandsaw, or the like.
The sensible option would be to hire a crane or a forklift to do the job, but cash is tight so at the appointed hour the truck turns up at the end of your driveway to meet you and as big a group of your friends as you could muster. You’re going to shift this thing with pure muscle power! If you grow up around any form of workshop-based small business it’s something you’ll no doubt be familiar with. Craftsmen seem to have a network for such moments, so just as the blacksmith might find himself helping the woodworker unload a huge saw bench, so might they both spend an unexpected afternoon at the engineering shop manhandling a lathe. 2 Pulley Block
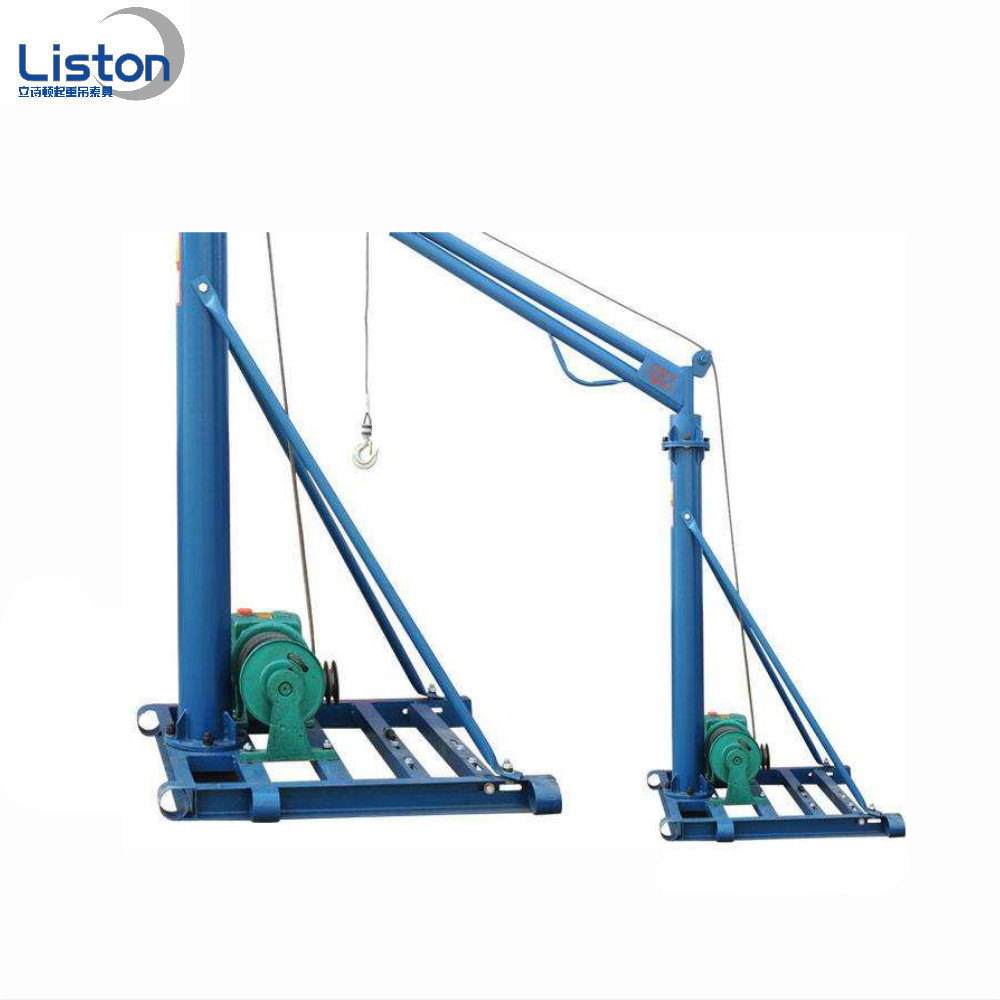
It came as a shock in a casual hackerspace conversation to realise how many times I’d been involved in such maneuvers at home, for friends, or at hackerspaces, and how that experience in doing so safely isn’t necessarily something that’s universal. Maybe it’s time to tell the story of moving big machines on limited resources. This is something that starts by thinking ahead and planning what you’ll need and where you’ll need it.
The armory of the shifting crew consists of a varied array of boards, blocks, wedges, thin pieces of wood, and long levers and crowbars, with jacks, ropes, straps, tensioners, and even the occasional chain hoist or winch if you have one. The key to success is not to plan the grand move in which somehow everything pivots instantly into place, but instead to perform a succession of achievable small moves. This way even the heaviest of equipment can be moved, maybe not with ease, but certainly in an achievable manner.
If you take a moment to imagine a typical truck with a machine on it, it’s a flat platform several feet off the ground. Getting the machine off the truck by hand is a task for a hefty wooden ramp and a lot of pulling and swearing with more than a hint of danger, so here’s the moment when it’s a smart move to forgo the muscles and make sure the truck you use comes with a loading crane. If this sounds odd when writing about moving things without cranes or similar then it’s worth remembering that this is about moving things when you don’t have the means to hire in extra mechanical help rather than forgoing it by choice.
Making sure your haulier has a loading crane is a smart choice that saves a lot of bother, and shouldn’t cost a huge amount more than one without. Even if you don’t have a loading crane all isn’t entirely lost, growing up on a farm I’ve seen more than one heavy load moved by suspending it from a tractor foreloader, or from an excavator jib. A friend even suggests getting in a tow truck for the job as they have a capable crane and are surprisingly inexpensive if hired for a short time, but maybe that’s something to discuss with your towing company.
A machine on the ground is just like any other heavy item that needs moving; it’s unwieldy, solidly wedded by gravity to the whatever it’s sitting on, and with a curious reluctance to move. If you have any sense you unloaded it onto a couple of planks over which you can slide it, but otherwise or if it’s something that’s sat for years in a forgotten corner of a yard, it’ll need lifting up to get something underneath. Easy with a crane, but still possible to do safely with ingenuity and simple equipment.
The key to lifting a heavy item off the ground lies in it being relatively easy to lift up one of its corners by a few millimetres with a lever or a jack, and then in repeatedly doing this on all corners while inserting thin wooden packing pieces to lift it off the ground bit by bit. Eventually a stack of the thin pieces can be replaced by a single block, and whatever planks, dolly, or other moving equipment can be slid underneath. It’s very important to remember never to put feet or other body parts under any large object lifted into the air in this way, something I once discovered the hard way by dropping an Austin 1300 on my foot. (It hurt a lot but by some miracle nothing was broken.)
Moving a heavy machine sideways without wheels comes back to those achievable small moves. Having got it resting on some planks, the key is then to lay a trackway of planks not unlike a crude railway, and lever the machine forward inch by inch sliding it along the planks.
My dad would do this by running straps from his building stanchions, then using an old-fashioned lever tensioner to shorten the strap by a small amount to move the load bit by bit. This is the point at which having all your friends over is a great idea, and you’ll be amazed how easy it can be to move a machine an inch forward when there are five of you.
Slopes can be negotiated with more levers and wedges to raise and guide onto fresh planks, and when the destination is reached the whole thing can be lifted into the air with wedges and blocks just enough to move the planks. The Shenzhen-based maker and YouTuber [Naomi Wu] posted an excellent video last year showing the whole process performed by a group of neighbourhood “uncles”, as they expertly moved her laser cutter from the street into her house.
It might seem an awful lot of effort to go to, but having the skills to safely move heavy machinery without extra drama can save a huge amount of bother and expense when equipping a workshop. It’s also handy for the reason my dad and all those other craftsmen found themselves handling large machinery in the first place, as people with an eye for a machinery auction bargain they knew that a very capable and useful machine can go for not a lot at the machinery auction if it’s old and heavy and looks too difficult to move. Perhaps it’s worth keeping a few planks and ropes handy, just in case.
PET or HDPE bottles/jugs have a fairly low coefficient of friction on a lot of surfaces… this means that if you can jack or lever something heavy just a little off the ground, and stuff a flattened bottle or jug under each foot or low spot, you can then shove it a lot easier over a flat surface. Might get your prize shoved to a loading dock or something where it can be handled better, or maybe it got dropped off at the end of your driveway and you need it in the garage.
Even wet wood slides well. A bit of fairy liquid whatever. I aim to have the highest friction that is easily movable as having too low a friction can be dangerous as once sliding things can start going where you don’t want them to. So just enough and no more!:)
I keep a spray bottle of water and dish soap in my crate of machine moving equipment. It comes in handy all the time to be able to lay down a slippy path ahead of a heavy thing.
For larger objects, you can make an indestructable hdpe sledge from an old poly barrel. I have one of these on the farm for dragging heavy, reluctant objects across the driveway, the grass .. etc. In fact, its the perfect tool when the cartage path traverses a variety of surfaces.
Costs about $10 in materials .. will last a lifetime .. goes over almost any surface, hard or soft, with relative ease .. and in most cases inflicts minimal damage.
If it’s a steel thing you could also use flat stock, steel on steel friction it’s low enought to move heavy machinery like a lathe or mill.
I had to smuggle a metalworking lathe into my barn while the missus was out. Part of the last 10 yards was across a lawn. I had some old painted wooden pine boards hanging around, which formed a nice walkway across the lawn, except that they only reaches about 4 yards,, so I had to keep moving the back one to the front.
She didn’t discover the lathe was there until about 3 months later!
“She didn’t discover the lathe was there until about 3 months later!”
I have moved a fair few machine tools (and expect to be relocating a Kearns S-type in the next couple of months) A chain hoist can be used on the floor. It’s no fun and the hand-chain will keep getting snagged, but it will work. A “Tirfor” style cable puller or lever hoist is better in this role. Also very useful is a good, big crowbar. You can use these to “walk” machines around. Down, sideways, up, repeat on your end of the fulcrum will inch the machine sideways. I have one of these and for the price there really is no reason not to have one at hand: https://www.screwfix.com/p/roughneck-gorilla-wrecking-bar-48/29330 (as some reviewers point out, a 48″ bar is bigger than is sounds) And, of course, rolling along on a number of pipes like the ancients (probably) did. Works well on relatively smooth surfaces.
If you have soft ground to negotiate, though, you probably can’t beat a telehandler.
Consider removing control wheels and handles that might be damaged in a tumble, and protecting the ends of the shafts left behind with lumps of timber or thick-walled tube.
When we were moving megawatt lasers at a previous place of employment, they had things like crowbars only with two small heavy duty wheels at the bend of the crowbar. They were built to take pieces of lumber as the lever, so you had a 2.5 meter board as the lever arm, the wheels as the fulcrum, and maybe a 4-5cm long steel wedge at a right angle to the board that could go under the edge of the machine. You could lift/walk almost anything with those.
These are commonly used in safe moving. Simple and highly effective.
I was installing a 35,000 lb machine that had to be lowered by crane and moved a couple feet to its final location. I cut a set of rollers from 1″ steel round stock, but the millwrights eschewed these and instead tapped the flux off a handful of 1/8″ welding rods, slid these under the machine, and rolled it into place with a light come-a-long. Experience is a wonderful thing.
In another venture, the Guatemalan Navy was guiding a group of volunteer well drillers to an isolated village to recon a well site. We had to drag a boat weighing over a ton over the beach to a backwater. The navy guys made a bunch of rollers out of driftwood and about 15 people hauled on a rope to drag/roll the boat 150 ft across the beach. We Americans got into full tug-of-war mode and consistently ran the boat off the end of the rollers instead of allowing the rollers to be cycled around to the front of the boat. The navy guys never said anything, but we drew stern looks.
Welding rods as rollers is genius.
As an engineer, I loved working with millwrights. The good ones listened to me when I was right and ignored me when I was wrong. And then there was their superpower of moving heavy stuff without breaking things.
Did you get a bow when it reached the other end?
Maybe they got stern looks…
That’s what Bstriggo said too! But, I wonder if they shared a bottle of port to celebrate?
Oh yes, you need to drill your helpers to “get out of the way and let it happen” if things start to go wrong, the second a large mass is uncontrolled, you need everyone out of the way of it, not trying to hulk or supergirl it back into compliance. “I do not want to clean your minced brain off the side of this thing!”
Ideally you’d want to constrain the degrees of movement, making sure that breakaways can’t happen, but it’s often a case of “No battle plan survives first contact with the enemy” and Mr Murphy never taking a day off.
100% and keep an eye people so that they are not in positions where should the machine fall they have no room to run or something ( or someone) to trip over.
Some pipe or rebar will let you roll a heavy machine. An engine hoist is pretty cheap and generally useful. I’ve moved several lathes and mill-drills with mine. You can rent roll-lifts. Wheels with a hydraulic or screw lift and ratchet straps. Used in pairs, one at each end. A proper come-along works wonders. Basically a long crowbar with a rollerskate on the end. Lever it up, move one end at a time. If you’re using a forklift or tractor into a garage with a low door opening, do not forget that tires will compress under load. You might get the forlkift in but the rollbar will be too high to get it out after you unload your mill. Experience.
“Basically a long crowbar with a rollerskate on the end.”
https://www.amazon.com/BestEquip-Prylever-Capacity-Wheels-Length/dp/B07SHL3H7L/ref=sr_1_3?keywords=rolling+pry+bar&qid=1667231965&qu=eyJxc2MiOiI0LjY5IiwicXNhIjoiMy44MyIsInFzcCI6IjMuMj YifQ%3D%3D&sr=8-3
Also known as a Johnson bar (one of many things with this name). I have an old one (Fairbanks) with an oak plank for a handle and large cast iron wheels. Large wheels are key on any but dead smooth surfaces.
“Grab your Johnson bar” sounds like… something else.
I trim their urls down to cutting everything past the “ref=”. Still works.
You don’t need the item vanity name either – this links to the same product: https://www.amazon.com/dp/B07SHL3H7L/
Thanks! (I owe you yet again!)
For items like milling machines and similar, you can rent hydraulic platform lift trailers like these:
https://www.sunbeltrentals.com/equipment-rental/0241700/8-9-lift-bed-single-axle-trailer-10k/
They allow you to load from the ground (roll) rather than lift.
Site Temporarily down for Maintenance, will be back up on 10/10?
Used to uncrate and position large 120KW TV transmitters which were delivered by movers in transmitter buildings. I’d show up with a small breaker bar, 5 or 6 (x) 3/4 inch steel rods, a rope, a small come-along and web strap. Generally a short job without breaking a sweat. Rebuilt a 9 channel FM combiner that was ceiling mounted. it’s amazing what you can do with block and tackle, come-alongs and redheads.
Another tip if you have to move heavier equipment long distance by hiring a haulage company -> whenever possible, prepare the machine by building a heavy pallet out of (thick) plywood and 4×6 or 4×8 beams (or use a standardized pallet if it’s big and most importantly strong enough). Drill holes through the base and secure your machine to it using nuts and bolts. make sure the bolts don’t stick out underneath where the forks will go. If they do stick out underneath, mark clearly in red paint where the forks can’t go or get some “Fork here!” stickers (couple of euros/dollars on online shops probably). If possible plan your runners such that the only good way to grab the pallet is in safe locations. Add (ratcheting) straps if needed to add stability. The pallet end can simply be screwed to the pallet with 3 or more screws. 2 is usually pushing it but can work if you add washers. A single screw will simply pull through the strap. Good chance the costs charged will be much cheaper if you can give the haulers a way to handle your load with standard equipment (forklift and pallet-truck). Also makes moving stuff around yourself easier, renting a pallet truck is fairly cheap usually. Make sure your pallet is wide enough that it can handle at least a minor amount of tilting/tipping, otherwise you might get the dreaded call they dropped your machine. It doesn’t need to be stable to 30 degrees slope, but you’ll want at least something like 10 degrees or so.
secondly, roller pinch bars (sometimes roller crow bars) are amazing for making final adjustments or getting that first small bit of lifting to install blocking or get stuff on rollers. If you’re only going a small way with a smaller machine, 2 roller pinch bars and a bit of muscle might be all you need.
I see [Naomi Wu]’s “uncles” using a hydraulic floor jack (for automobiles) in that video. I probably wouldn’t have thought of that.
You can use an automotive hydraulic jack horizontally too, as long as the pump / valve assembly is at the bottom so the oil flows into it.
I’ve used a harbor freight portable hydraulic pump/cylinder to shift stuff at home. And the aforementioned engine hoist.
You can even use more than one to lift and roll things. Moved a huge swing set that way. Good reason to pick up a cheap “racing” (aluminum light weight) floor jack when you see one on sale.
Toe jacks are a lifesaver too, bought a couple to move a big lathe and they ended up being one of my go tos for getting things high enough for machine skates to slide under. Johnson bar -> toe jack -> machine skate… Then back again to get it onto the floor.
TEMCo Hydraulic Container / Machine Toe Jack (5 -10 Ton) Lift Capacity TH0023 https://a.co/d/i6B7wNc
British English “tractor foreloader” USA English “front end loader”
Also, don’t trust the ratings of Chinese equipment. Lifting gear _should_ be plated with the Safe Working Load. Chinese engine hoists are plated with (at a guess) the breaking strain of the best of the prototypes before they found a cheaper supplier of thinner section steel. This is my 2-“ton” engine hoist after attempting to lift my lathe, which the manufacturer docs state at 750kg. https://photos.app.goo.gl/DNs2rqu8Fb9pBdPW8 But, in a bit of a “perfect storm” Holbrook seemed to like to under-state the weight of their lathes. An owner in the US weighed his 750kg “Minor” lathe at 1247kg (with the tailstock removed) with a calibrated dynamometer.
One of the points with engine hoists is that they de-rate the lifting capacity as the boom is extended. On the hoists I have used with the boom fully retracted they were rated to 2000 Lbs. At the second hole it was rated at 1500 and the 3rd hole down to 1000 and the 4rth was 500 Lbs. Some hoists may not show this on the side of the boom, but, it may be listed in an owners manual. (Whats an owners manual?) https://www.knockoutengine.com/torin-t32002-engine-hoist-with-load-leveler-review/ Look at the ratings for the boom.
Yes, I am aware of that, and was lifting 750kg (maybe really 1250kg) in the 1.5 ton (1500kg) position. The ratio of rated load to failure load for lifting equipment should be at least 4.0, not, as in this case less tha 1.0
I fully concur. It should not have buckled the way shown in the picture at that load. It also looks like only one leg buckled. Is it possible that the weight distrubution was uneven? Engine hoists are made for lifting basically centered weight as the engine and or engine/trans are typically in line with the hoist.
It was hanging from the hook. There isn’t really any way (on level ground) to load the unevenly.
Another reason you might overstress your lifting equipment is illustrated by the humorous alt definition of an engine hoist…
“A device for testing the tensile strength of everything you forgot to disconnect.”
So yah, get a hangup, don’t power through it, investigate.
Yes, that ^. Many a ground cable has impeded my progress over the years. The tensile strenght of a 4 AWG wire is astounding!
Using a come along (wire rope hand ratchet puller) to pull things around.
It expects me to sign in to see the image.
All of those folding hoists with the telescoping boom and splayed, folding legs are junk, even the best of them. The reason the upright is angled back and has the side braces and six wheels is because the design is fundamentally flawed. The telescoping boom is a big weak point, so are the hinges in the legs and the pins that hold them down. All that keeps the thing from bending in the middle and falling forward is the shear strength of those two pins and the tear strength of the metal they go through.
The best portable hoist is a BlueBird KayDee series. I have a KD1500 made by the original company. https://www.icfinc.com bought them a while back but appears to have recently discontinued the product line and/or sold it off. They’ve removed all info about the hoists from their site. :(
The number in the model indicates the rated working load, which is always at the full boom length since it doesn’t telescope. Mine has on occasion easily lifted more than 1500 pounds.
But since the things are indestructible there are many available on the used market, or find a rental company selling one.
They’re built from 1/4″ wall (or thicker) rectangular and square tubing, solid metal wheels, and heavy steel plate. The legs are parallel and slide into sockets at the ends of the cross beam, secured with a captive pin. The upright simply slides down into a vertical socket. The boom hooks onto a horizontal rod at the top of the upright then the hydraulic cylinder bottom hooks onto a horizontal rod about halfway up the upright. The end of the piston slides into a pivoting socket on the underside of the boom. The separate pieces are each low enough in weight an average teenage boy can assemble it. IIRC I was about 14 when I was able to fully assemble it without help from my father, and I was a weedy kid about 5′ 5″ tall.
They made a Tip-Tow series with large wheels behind the base beam, a trailer hitch, and pins to hold the parts together normally held in place by gravity. They could be left assembled then tipped backwards, legs in the air, to be towed behind a truck. IMHO if your work truck is so full you’d need to tow an engine hoist behind it, your work truck isn’t big enough. The knock down models will fit into many cars that have a fold down rear seat.
The UK equivalent of what you describe is probably the Epco one (an example here https://www.ebay.co.uk/itm/234747177026 ) but they take up a lot of space for something only used avery couple of years.
Hey! I have one of those, but the ram is knackered. One day, I’ll recommission it.
I can confirm that the Epco will comfortably lift a Holbrook Minor lathe in exactly the way that the cheap Chinese crane didn’t, having recently shifted someone else’s Minor who happened to have an Epco.
Wow. The material in the damaged leg looks to be a thinner guage steel than that of my own Chinese engine hoist with the same rating. Material consistency and quality control is always a concern when you’re dealing with Chinese sources equipment. I certainly wouldn’t trust my life to the advertised load capacities on such equipment.
I can recall one time years back when a 2-ton Chinese cable come-along failed well below it’s listed load capacity and in doing so actually saved me from serious injury. A friend and I were trying to bring an old 70s dirt bike back to life over a few beers and had been trying to kick it over all afternoon and the kick start eventually failed. Push starting it seemed like too much work in our condition so we decided to instead hook it up behind his truck with a 2 ton come-along and pull start it on the roads around the farm. It didn’t want to fire but I continued adjusting the carb and playing with the choking until it unexpectedly fired up, jumping forward a few feet removing tension from the tow cable then immediately died at which point the 35 mpg tow vehicle pulled the slack out of the line yanking the handlebar right to full lock position, dumping the bike on its side and pinning me beneath it and the gravel/concrete roadway. Mercifully the come-along failed after only a few feet of being dragged. Which is a good thing because by inebriated friend kept right on driving totally oblivious. If that come-along hadn’t failed at a fraction of it’s rated load capacity I might have been along for the ride for a couple miles.
Definitely wouldn’t trust my life or safety to economy imported tools/equipment.
This is why girls live longer than boys. LOL
Instead of a tow truck, get a ramp truck. They are rated for at least 4 ton, can extend to touch the ground, have a winch to drag stuff up the ramp, come with some tie downs for heavy objects, and best yet, another set of hands that is used to moving heavy inert lumps. We used one to move Dave’s van Norman universal mill. (~2.5 tons)
Next, you want dunnage, aka cribbing. Rough cut hardwood typically 4-5” (20-25cm) thick, and at least 1.2 meters (4-5 feet) long. (Long ago pallets for shipping paper had two such pieces as the risers). You can rest a machine on them to allow you to get a jack, or fork blades under them, and you can use them in a jenga like stack along with bottle or scissors jacks when you need to change the height of an object. Jack up a few inches, add dunnage, Then reposition jack one block higher and repeat. Yes it takes patience, but that is the most useful thing you have when confronted with a big lump.
The best option I have found when confronted by soft ground is sheets of steel plate. Since it isn’t spanning a gap, 10-12mm is usually sufficient. When I last moved, I scored 3 4×10’ sheets of 3/8” scrap steel diamond plate. (Former trailer beds) the Bridgeport clone rolled across it nicely.
If you have bottle jacks and tools to manipulate heavy plate steel, you can convert them to toe jacks. (They lift from floor level)
One thing many home rigging crews may face is the advanced level – bulkhead basement stairs. It’s why I put “walk out shop space” near the top of my wish list when we were looking for a house. (And decided instead that the next move would be an occasion to replace the lathe and mill, as my current pair are sufficiently tired that they wouldn’t be worth the effort needed to get them back up the bulkhead stairs)
“The best option I have found when confronted by soft ground is sheets of steel plate. Since it isn’t spanning a gap, 10-12mm is usually sufficient. When I last moved, I scored 3 4×10’ sheets of 3/8” scrap steel diamond plate. (Former trailer beds) the Bridgeport clone rolled across it nicely.”
And when you’ve got a lot of weight on small diameter cast iron casters, everything is soft ground. Concrete not specifically poured to be a machine shop floor (And even then, crap happens) may have large enough voids near the surface for high pressure on small wheels to punch through and topple the whole shebang over. Similar cautions apply to plywood, which can be seen to crush under the load and may also have voids that cause sudden spills. It’s not so bad if you’ve got something with pneumatic tires spreading the load a lot more.
Asphalt should be regarded with suspicion… it’s the pitch drop experiment as a surface, in hot weather it might be positively gooey. Even in cold weather, you might take a break moving something on it, come back well stuffed and lubricated and the stupid dolly is up to it’s axles.
Good points. I don’t use casters (save the fairly large ones on the Johnson bar). My default is 1 inch schedule 80 black iron pipe. (No, the big box places don’t carry it, you have to hit a plumbing specialist). It’s a bit over 1.2” in diameter, has heavy enough walls to cope with machines up to 2 tons. It’s cheaper and a bit easier to carry than option 2, 1.25” hot rolled round. Option 3, cut the bolt flanges off of broken semi axles. (Usual break is right after the splines, so they should be priced by the pound). You don’t get the same range of lengths tho.
As for concrete, last two shops had pours dates at least 60 years prior, so they had cured enough that they would resist a powder actuated driver, unless you used a strong (#4 or 5) load. I also spent $100/gallon on actual industrial epoxy floor coating. (“Rated for moderate forklift traffic”). Stuff rolled just fine, but the heaviest thing I moved was the bare base of the mill ~850 lb.
All good points. For tracks on ground, I frequently use 2x-whatever planks with 4 inch heavy wall aluminum rollers(scrounged). For dunnagd, every time I see cutoff of 4×4 or 2x-whatever, I muckle onto it & goes into a pile; i never have enough.
You can go old-school. Very old-school. xhttps://www.youtube.com/watch?v=E5pZ7uR6v8c&t=324s
Haven’t needed to move a heavy lathe (yet) but most “real iron” machinery can be disassembled down into smaller more manageable pieces. All relative though. I moved a big floor mount drill press alone by taking off the motor and taking apart castings etc. much easier to love several <100 lb pieces than one big monster. Reassembly and alignment would be a pain but if you're doing it on the cheap, may be an option. Also learned- moving even relatively lighter loads with all the techniques listed above is better than manhandling. Example: the big motor probably weighed … oh 50-60 lbs? but putting it on a floor dolly to move it the 20 feet to the pickup was better for my back (and safer) than just going diesel and hauling it directly in my arms.
One should probably consider complete realignment as part of the deal anyway. It’s amazing how much a cast iron frame will shift. All the jouncing in transit will have an effect. So really nothing lost by disassembly… unless your helper throws out the “Airplane parts”
I sold a Hardinge lathe to a guy who rented a van (Ford Transit or Dodge/Mercedes or similar) and the tallest one he could get had a rear door opening less than 1″ too low to slide the lathe in with the bottom at the floor level. So he had to spend a while on my shop apron taking the lathe apart. He was going to have to take it all apart anyway to restore it.
“[…]much easier to love several <100 lb pieces than one big monster."
That's what she said… :D
“[…]much easier to love several <100 lb pieces than one big monster."
That's what she said… :D
There is a picture in an old National Geographic on India that shows a nuke reactor vessel being moved up two or more stories into the building on railroad tie cribbing. One layer at a time safely. No big cranes.
I’ve moved pianos into the second floor or organ over the railing to the choir loft with a hand cranked winch tower like holds speakers at a show. Rented it locally.
When I was in the hospital, they had things to hoist me out of bed. Slip a sling under me, press the remote, and it would lift me. Fun.
Those bed hoists sometimes come up for sale cheap and are worth considering vs a horror freight engine hoist.
Not as big a horror as someone weighing as much as an engine.
I’ve thought about getting one of those hospital patient mover lifts and rails for my shop. I look at the safe load number and think that’s about what a small block Chevy or Ford V8 weighs. How the heck can it lift that much with that aluminum track??? Would be cool to have rails running around to pick and move heavy stuff.
We have covered 3 of the elements, Earth>Iron Bars, Water>hydraulic equipment Fire>Internal combustion powered machinery but what about Air?
Something which may give you a start, particularly if the only area you seem to be able to get a lever into seems suspiciously like “soft underbelly” vs the hard structure of legs, that are flush with the floor, is a high pressure inner tube…Stick it under, or in the gap against the wall because you need to ease it out or something, just to open up enough room for other methods… then pump it up… if you’ve got all day or no power, with a foot pump even… Though use caution as it’s not an inherently stable kind of jacking method, and you don’t want a 500lb safe or something bobbing around on top of a rubber spring.
A friend talks about the time they moved a 10 tonne mill with air – some kind of skirt around the edge of the machine and pumped it up like a hovercraft. Apparently it slid like a hockey puck and but they were well warned that it still stopped like 10 tonnes of granite and steel, which is to say it doesn’t stop, so don’t stand between it and the wall. There was a dead man’s switch on it to drop it in an emergency.
CFM required for those air pucks is extreme, most of us would have to rent a towable screw compressor for them.
If you want a fun read, hunt up a copy of “Moving Heavy Things” by Jan Adkins – nothing like getting a newly finished sailboat out of the barn to make you consider wild ways of moving awkward, non-rectangular stuff. It also includes the legend of the bacon strips….
I spent a summer in grad school earning extra cash by moving heavy equipment with some guys who were consummate pros at the whole thing. Not much for formal education, but they showed me how to move just about anything with pipe rollers, wheeled dollies, blocks and tackle, “jawbreakers” (lever dollies, nicknamed because if they got away from you the lever end would flip up and hit you under the chin) and an absence of urgency. It’s served me well ever since.
Jack up one side, insert a slightly off center pivot point, lower it onto the pivot, rotate the object in the direction of travel, repeat many times. As long as the friction is nice and low, you only need to lift the difference between the two sides of the pivot point.
You’d be surprised how easily about 1,000 pounds of circa 1914 Sears Expert* 14″ swing metal lathe slides on a smooth concrete floor, with only two people pushing. The feet pads on the bottoms of the cast iron legs were pretty small so there wasn’t a lot of friction.
*According to the contemporary advertising, Sears Expert lathes were made by an “old, reliable” company. That was South Bend Lathe, founded in 1909. “Old” was 5 years in 1914.
Come to mention it though, truly ancient equipment does have more what you’d call pads, like rounded, circular buffer stops almost, of reasonable size as if they were intended to float it on rammed earth floor or something.
There is a reason why I have a hydraulic lift table cart- I’ll need to occasionally rack or de-rack Heavy things like disk shelves, large UPS units, etc. and it’s been a back saver for me, especially if I’m doing it solo.
I also have a small winch rated for 2500 pounds bolted to a 4×6 plank that I can strap down to the top of the bed of my truck using slings and webbing; I also have a ramp for the bed of my truck, and it’s for the same reason I have the lift table cart. (I also have a number of furniture dollies and a couple hand trucks.)
Other things that I keep in the truck’s ‘cargo handling’ bag include a handful of ratchet straps, the aforementioned slings (along with a tow strap capable of pulling the truck), shackles, and a pully.
I also have a kit for use with the hand truck for lashing down stuff, which is mostly paracord and the Nite-Ize “CamJam” devices, along with some climbing rated carabiners.
More hackish, put heavy stuff on fulcrums and pivot points. This may have moved ancient stone blocks.
On a related note, here’s someone who moves 20-ton stone blocks by hand: https://youtu.be/E5pZ7uR6v8c
Ninja’ed by Patrick by 3 minutes. :-/
No mention of Leed-Skalnin and Coral Castle?🤔
Come to think of it. I am a little disappointed in myself that I don’t have a Thunderbird 2 type road vehicle, with a demountable Pod #3, in which I have something like remote controlled elevator cars, that can just be driven up to what I want to move, then flop it over onto them…
Don’t underestimate the usefulness of a low-clearance automobile floor jack. They usually have two iron casters at the load bearing end and two swivel casters at the other end, a load capacity of 1.5 – 4 tons, and are easy to find.
On the topic of moving heavy things, I found this video about how to move a rail boxcar quite interesting. The device has a foot that jams between the bogie wheel and rail, whilst the handle operates a force multiplying lever heel that pushes against the wheel. https://www.youtube.com/watch?v=7W8c_jMVYAs
The ‘Appleton boxcar mover’ seems to still be a thing and there are plenty of vintage ones on that usual auction site. I once thought about making a smaller and wider workalike mover from square aluminium bar stock to wedge under the tyres and move a caravan around, but ended up fitting electric motors instead.
For a surprising number of times, for me the answer to “how am I going to get this upstairs”, has been to just accept that this is going to be unpleasant and include some swearing, find a somewhat possible grip on the lump, and just manhandle the thing until the job was done and celebratory beverages could be had.
“just gettir done” failed me recently however, when my newly constructed, and quite substantial shed (think 5.5x4X4m section of inverted boat, clocking in at 2 tons) was slowly sinking into the filled ditch it turned out is was build on. I had to move the building 40cm back and forth to replace 2 foundation piers, and given it was wedged in between a substantial fence, it was not going to be easy.
I tried digging in bottle jacks to lift it, but that only succeeded in pushing about a meter high stack of pavers into the ground, never to be seen again.
the answer turned out to be dunnage bags, inflatable woven PP bags that are normally used to take up space in a container. with 4 of these on each corner, the building rose clear of its foundations with relative ease (just a substantial amount of clenching), rollers could be inserted, and the building pulled along using big ratchet straps. did it alone in just 4 hours.
the way back however, the weather had turned into cold and wet, which the bags did not like. they showed their displeasure by exploding a lot. this proved very exciting but unproductive. it took 2 people 3.5 days and much wailing and gnashing of teeth to get the shed back in place.
I paid a tow truck $75 back in 2001 to lift my Bridgeport mill off the delivery trailer when I bought it. The pucker factor was huge when it picked it up. The boom retracts when it lifts, and it had to drag the mill off the trailer a few inches. Then the mill swung like a fast very heavy pendulum for a few seconds till we got it stable. My garage is in my basement, so the truck drove it down my driveway. Of course, it would not fit thru the door. I had planned ahead and bought several 1″ pieces of iron pipe which we used as rollers to roll it into place. Luckly the tow driver was a huge strong guy. He, a friend of mine, and myself man handled it into place. Have not seen that friend since now that I think about it. When I bought my lathe, the guy brought a forklift with him. Then we man handled that into place because the forks were too tall. Fun times, but worth it.
You should look into some of the equipment and techniques used in the safe and vault industry where moving heavy equipment in challenging conditions is a routine. Over thresholds, up-down stairs, over expensive and easily damaged flooring, in and out of tight spaces with limited access, etc. Cribbing, roller pinch bars (Johnson bars), piano dollies, specialized stair climbing equipment, even hover pads/skirts that allow several tons to ride on a cushion of air and be maneuvered by single person over carpet, thresholds, etc. Safe movers have been seriously injured and even killed by tipping or sliding safes – in the moment it’s easy to underestimate the forces at play when a 2000+ lb safe moves in an unattended direction and you instinctively try to halt that movement… Since keeping a heavy safe balanced and easily controlled is key to a safe moving operation, one of my favorite pieces of equipment are known as SlikStiks. The system is based around 4′ length, 2″ wide, foamed padded wooden planks that are topped with 1″x1″ PTFE sticks which are tapered at each end. The basic kit also includes a flat “sled” which is basically a large, heavy duty, 1/8″ thick PTFE sheet that can be slid beneath rough bottom safes which then slides along the sticks. If the safe has a relatively smooth bottom then only the sticks themselves are necessary. You basically just lay the sticks out and create a travel path for the safe like a railroad track. The system can support any amount of weight by increasing the number of sticks (on a heavier safe simply add a third “rail” between the outside sticks). Most safes slide relatively easily and are stable and balanced during the process. For maximum effect I’ve occasionally used a silicone spray lubricant applied over the sticks prior to the move. When this method is used a safe will literally glide along the sticks when placed in motion with a firm push. The silicone coated PTFE sticks are actually so “Slik” that it can be easy to overestimate the force needed to get a safe in motion and having it essentially run away from you. In one instance I had an 800 lb gun safe glide down a silicone coated 12″ foot track and continue right off the end falling flat on its face after being given just a short push.
A buddy calls me up one day and declares that the local liquor store offered him a safe for free!!! All he had to do was move it. I was the friend with the big pick up truck whom was going to help him move said safe to his apartment. I agrred to look at the safe and let him know if it could be moved. My pick up truck was a Ford f-250 which is a 3/4 ton truck. The elevator in his building had a 2000 Lb rating. Upon inspection of the safe I found the plate on the back. “2.5T” He didn’t get the free safe. Just in case you don’t understand “2.5T” is 2.5 tons meaning 5000 Lbs.
Note to self, category crime, subsection planning the perfect heist, entry number 27: Safes are heavy.
Forgot to mention the safe was 3 FT high 2.5 FT wide and 1.5 FT deep.
The old “you can have the safe for free if you’ll move it out of here” offer. You would not believe how often safe techs get this call. To the caller it seems like a really generous offer but the reality is that safe moving is very difficult and labor intensive and most safe shops already have plenty of safes to sell and don’t need another used safe sitting in their warehouse that would have to be completed refurbished before reselling anyway. The truth is that 95% of the time the value of the abandoned safe is a fraction of what the shop would charge to move that safe out. People are surprised to find out that they’ll need to pay the shop to remove their safe and haul it away. Even if you somehow managed to move the safe out yourself and brought it to the safe shop you’ll often find that they have no interest in taking the used safe off your hands because the time & cost of refurbishing the unit exceeds the potential profit from reselling it. In this case it’s essentially a 2 ton mass of steel and concrete with no scrap value that the shop will eventually have to haul out to a landfill and pay by pound to dispose of.
On a side note, any UL rated commercial, banking or jewelers safe is an order of magnitude more secure and reliable than practically any residential safe. A huge gun safe with large diameter, chromed bolts sticking out the top, bottom and sides of the door might look imposing but removing the inside door panel will reveal that the actual locking mechanisms and hardware don’t match the stout outward appearance. Gun safes might have an ETL listing or UL RSC rating at best and neither of these standards have any real security requirement. A residential gun safe is basically just an expensive gun cabinet offering some level of fire protection. The UL listing requirements for commercial and banking safes (B/C rate, TL-15/30, etc) means they met strict design standards and were specifically tested against forced entry and burglary. If this type of physical security is important in your application then a used commercial safe makes a great alternative to residential units – cheaper, more secure, more reliable but not as pretty and not necessary offering fire protection.
I would hope that apartment is on the first floor.
The apartment was on the second floor and the safe was 100% steel. None of this concrete filled rubbish. The safe had an outer door with combination lock that was about 6 inches thick and an inner door that was about 1/8 inch thick with a key lock. It was one of the most beautiful safes I have ever seen with gold leaf pinstriping on the outer door and an italian grape motif painted on the inner door. It was probably from the 1920-1930.
Too bad. I always work on the principal of “if it got in there, it can be gotten out” that has to be balanced against what will it cost, how much effort will it take, and how badly do you want it?
Addendum: that being said I once turned down a free arc welder because it was a 440 volt 3-phase motor-generator unit on the 2nd story of an old building that did not have an a built in lift rig. Thingbwasvfrim the ’30s-’40s. I suspect they got it up there with a block and tackle and a lot of muscle when labor was cheap. And at my residential garage I did not have a source of 3-phase power, and the cost of s convertor was not worth it. But if it been a single or on the ground floor, I would gave taken it. I am an inveterate scrounger, but sometimes you just have to pass.
Getting things out can get very difficult. My current mill and lathe will be included when I sell the house, I decided that the bulkhead stairs were going to be a one way trip.
But that isn’t the best story. Back when I was in high school (long enough ago that avocado green appliances were a thing) the high school physics teacher pissed off the football team. He also drove a fiat 859 spider. (735 kg, before rust lightening)
Over lunch one day about 12 kids fitted straps, cross boards, etc, and carried it into his classroom/lab. On the 4th floor.
To get it out, the riggers removed the windshield, tires, and one bay of windows. They tipped it on its side, and slid it out the window, where a crane, slings, and a guy in a bucket truck lowered it to the ground.
No clue what it cost.
I’m fortunate that I have a friend, next door, that has a couple of fork lifts. Popped a big hole in my driveway when moving my lathe off of a trailer. Apparently they didn’t remove the stumps before pouring the driveway concrete.
He almost tipped over the forklift when it stopped at the incline at my overhead door. I cringed as I watched my mill teeter on the front wheels of the forklift, but he knew what he was doing and recovered gracefully.
That being said, don’t ever cheap out on lifting equipment. It’s always a lot cheaper than even a short trip to the hospital.
My Dad moved a large Bridgeport style mill *by himself* at age 87. I suspect Mother was in attendance as a spectator, on her insistence, lest he get hurt.
Electric winch, tilting trailer and pipe rollers. We never discussed it, but I knew Dad well enough to immediately know how he did it when I saw the machine. I eventually found the pipes rollers.
Never under estimate the cunning of old men or women when they want something.
Rollerskates and airbags… Not literally, but pretty much what the devices look like that are quite often used to lift and move cnc machining centers or other beastly machinery. Air jacks, snatch blocks, pulleys and honkers… EASY!
One thing to keep in mind. Cast iron weighs 450 lb/cu ft, or 7200 kg/cu meter, 7.2 kg/liter.
Other useful heavy-thing-shifting items to have are the Burke Bar (the crowbar’s much larger angrier cousin), toe-jacks (a way to lift a heavy object via wedging under the tiniest of available corners), and the fam-jack/jackall (a ratchet jack like a toe jack with extreme height capability).
I moved some big stuff this weekend. A Kearns boring machine (29 cwt, whatever that means). I used the frame that I built to move my lathe (which needs to be pulled away from the wall for routine servicing). It is 4 beams that bolt together with heavy duty castors on jacking mounts. To link the frame we made some hooks from steel strap and drilled/tapped some M12 holes in the base casting. It would have been nice to find a way not to modify the machine, but we had one day to clear out the workshop enough to shift it (including moving a lathe, shaper and universal grinder out of the way)
https://photos.app.goo.gl/vDZFp8HmN6rvruy56
AIUI, cwt means “hundred weight”, so 29 cwt would be 2900 lbs.
Except this is a British customary unit. 1 CWT is 4 qtr or 8 stone, 8×14 lb = 112 lb. (20 cwt is one tonne aka long ton or 2240 lb, which is actually close to the 1000 kg metric ton), 29 cwt is 3,248 lb.
Please be kind and respectful to help make the comments section excellent. (Comment Policy)
This site uses Akismet to reduce spam. Learn how your comment data is processed.
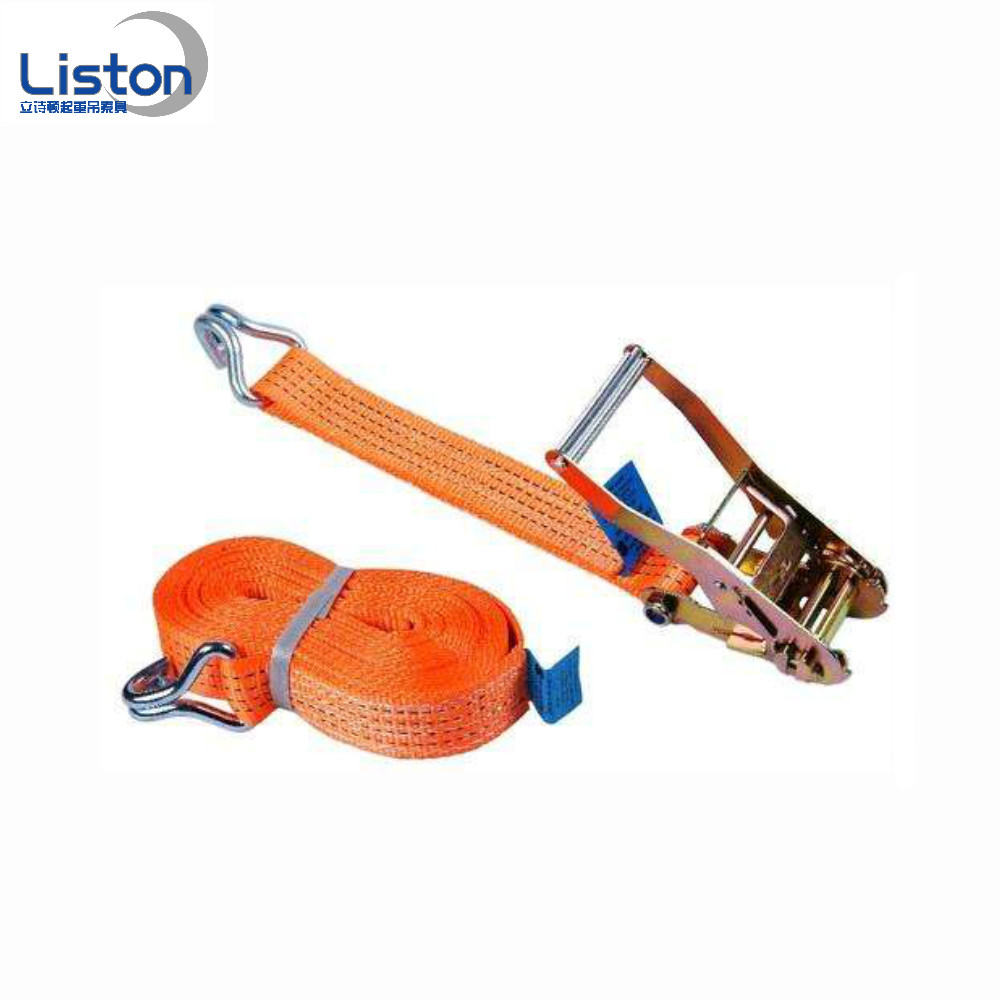
2 Jaw Wheel Puller By using our website and services, you expressly agree to the placement of our performance, functionality and advertising cookies. Learn more